Soenen Golfkarton keeps their corrugated cardboard production under control with Paessler PRTG
About Soenen Golfkarton NV
Founded in 1949, the Belgian company has a long history of producing high-quality cardboard products. Soenen Golfkarton NV is known for its commitment to sustainability and environmentally friendly practices in the packaging industry. They offer a wide range of packaging solutions, including custom-designed corrugated cardboard boxes and other packaging materials to meet the diverse needs of their clients. With a focus on innovation and customer satisfaction, Soenen Golfkarton NV has established itself as a reliable and eco-conscious player in the packaging market.
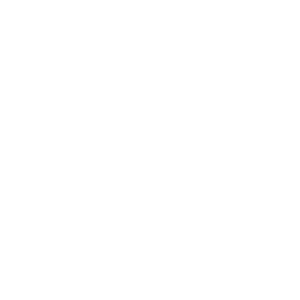
“We also considered other software. PRTG stood out because of its user-friendliness, flexibility and minimal consultancy investment.”
Wim Vandenberghe, ICT Manager, Soenen Golfkarton
The challenge
A cardboard box is not just a cardboard box, especially for Soenen Corrugated Cardboard. With a turnover of more than eighty million euro per year, this Flemish family business designs, produces and processes more than 300 million custom-made cardboard boxes every year. In order to be able to handle these numbers and keep all customers happy, the production process must run as smoothly as possible five days a week, 24 hours a day. The machines must work, the transfer cars must continue to operate in the factory and customers want to know exactly when their order will be delivered.
When Wim Vandenberghe (ICT Manager) and Vincent Seys (Network Engineer) joined Soenen in 2017, they immediately noticed instability on the network. Wim explains: "Applications and hardware all gave messages, but all separately, so we had to search through hundreds of e-mails to find the problem. It was always only afterwards that we saw that something was going on within the infrastructure. For example, if there was a network problem, it was quite a challenge to find the culprit. It often took half an hour to an hour before we knew where the problem was."
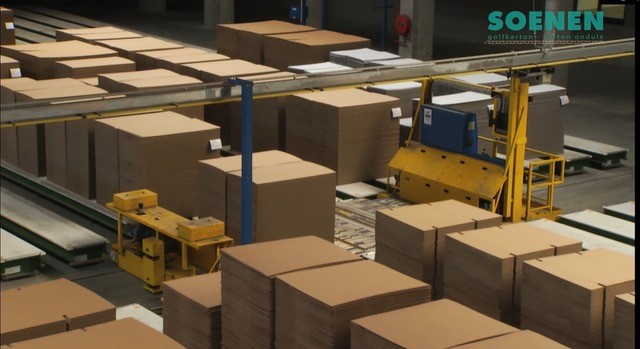
PLC network monitoring
There were also some issues in the PLC network. Wim says: "Machine control is becoming more and more ICT-driven. Cardboard is produced and ends up on a transfer car that automatically transports the cardboard further within the company. This transfer car communicates over a Wi-Fi network. The transfer car has a receiver, an inverter to Ethernet and a computer. At the end of the rails there is another antenna (transmitter). The communication with the transfer car was often lost, without us knowing what didn't work: the WiFi signal, the receiver or the transmitter?"
The ICT team decided to take over the management of the PLC network and to find a way to monitor this together with the rest of the infrastructure.
Centralized system and preventative action
Wim and Vincent were looking for a centralized monitoring system with which they could take preventive action.
"In the past, production sometimes came to a standstill. We wanted to reduce this in any case and at the same better inform users, such as office employees and colleagues on the shop floor, about possible problems. We also considered other software. Paessler PRTG Network Monitor stood out because of its user-friendliness, flexibility and minimal consultancy investment. Using scripts, we have certain tasks carried out automatically if something threatens to go wrong. Reseller Road2Result did the initial implementation and turned out to be very well aware of all the possibilities of PRTG. After that, we started experimenting with adding sensors ourselves and that was very easy," says Wim.
Time left to focus on other projects
Since using PRTG, the ICT team has noticed a world of difference. Thanks to "maps," they have a complete overview of what's going on within the company.
Vincent explains: "If, for example, a server starts to behave strangely, we see this on the PRTG app or on our information screens and we take proactive action. And for the entire network, the following applies: everything runs more stably, because we intervene before a critical problem arises. The number of interventions outside office hours has fallen by at least 40%, and the time it takes has even fallen by 75%. We now have more time to concentrate on other projects."
Conclusion
Peace of mind and time are not the only benefits of PRTG. The ICT team can now show the management that they have insight into all hardware and processes. As a result, they are allocated budgets more quickly.
Wim explains: "We recently replaced all switches in the network. We knew exactly how many switches we had, where they were located, which fiber connection, which VLANs etc. This made it easier for us to draw up a budget. We can now demonstrate that we can keep the project manageable and implement it quickly with minimal manpower."
Get to know more happy PRTG customers
Customer success story The Social Hub & PRTG
With the implementation of PRTG, The Social Hub can monitor each hotel location in Europe while simultaneously having a central overview in Amsterdam. ➤ Read the complete customer success story now!
Customer success story SKY Perfect JSAT Corporation & PRTG
Multi-channel pay TV operator SKY Perfect JSAT installed PRTG for traffic monitoring within its satellite communication services. ➤ Read the complete customer success story now!
Customer success story Abu Dhabi University & PRTG
With PRTG undertaking the day-to-day monitoring, the IT team at Abu Dhabi University now has more time for strategic projects. ➤ Read the complete customer success story now!